Injection of plastic parts is a manufacturing process widely used in the industry to produce high-precision plastic components in large volumes.
Plastic Injection Process:
Mold Design: A steel or aluminum mold is created with the exact shape of the part to be produced. This mold consists of two parts: the cavity and the core.
Material Feeding: Plastic granules, known as resin, are loaded into a hopper and fed to a heating chamber.
Melting and Mixing: The resin is heated until melted and mixed to ensure a uniform consistency.
Injection: The molten plastic is injected into the mold at high pressure through a system of channels and gates.
Cooling: The plastic in the mold cools and solidifies, taking the shape of the mold.
Demolding: Once the plastic has cooled and hardened, the mold is opened and the finished part is ejected.
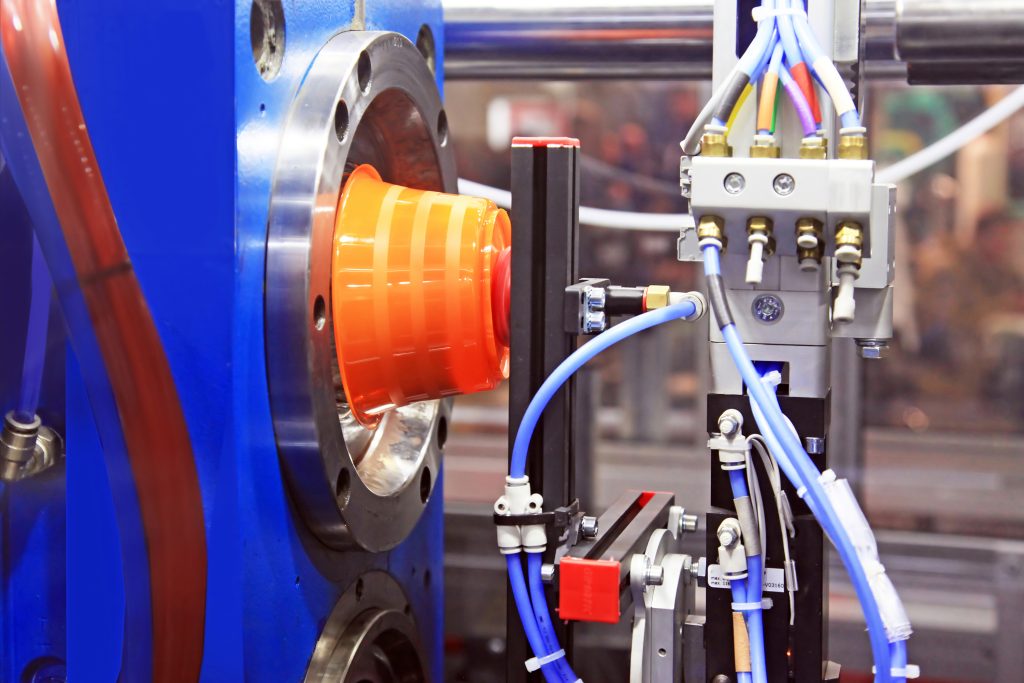
Advantages of Injection Molding:
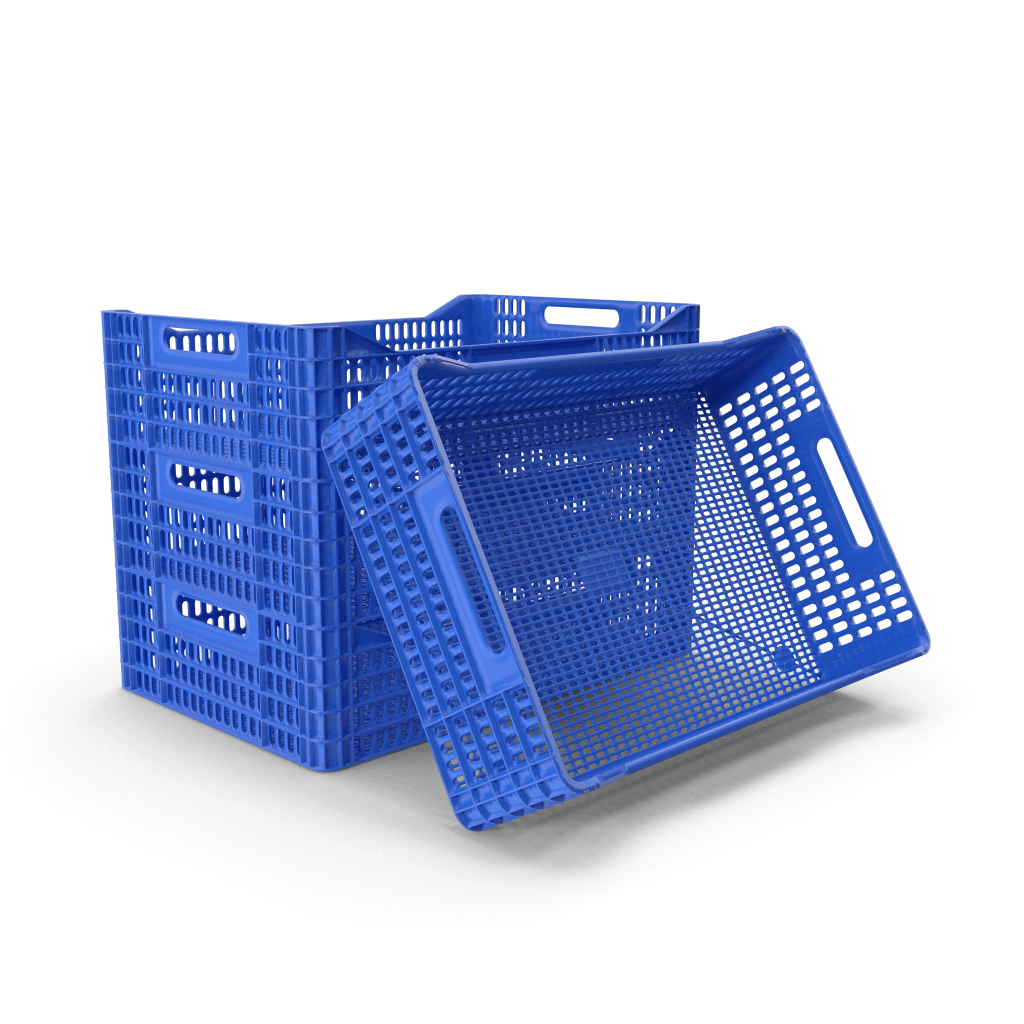
- High Precision: Allows parts to be manufactured with very tight tolerances and complex details.
- Production Efficiency: Ideal for mass production, since each injection cycle can produce several pieces.
- Material Versatility: Various types of plastics can be used, including thermoplastics and thermosets.
- Less Waste: Material waste is minimal and often recyclable.
Añade aquí tu texto de cabecera:
- Automotive Components: Instrument panels, bumpers, and internal components.
- Electronics: Device housings, connectors and internal parts.
- Medical Products: Syringes, medical equipment components and disposable products.
Consumer goods: toys, kitchen utensils and packaging products.
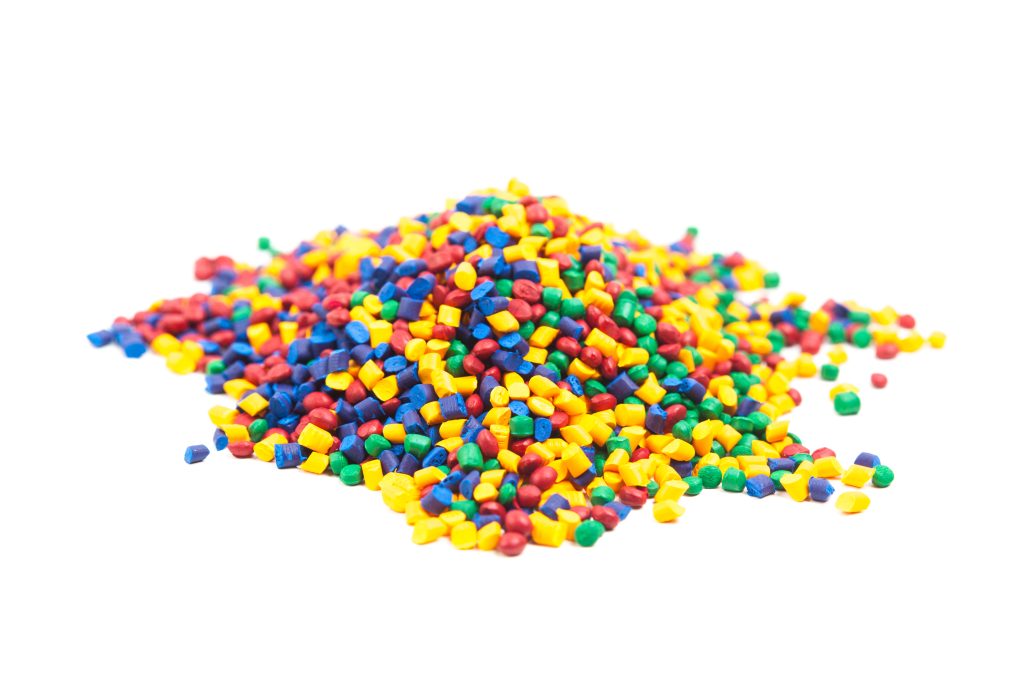
Considerations:
- Costo del Molde: La fabricación de moldes puede ser costosa, por lo que es más rentable para producciones de gran volumen.
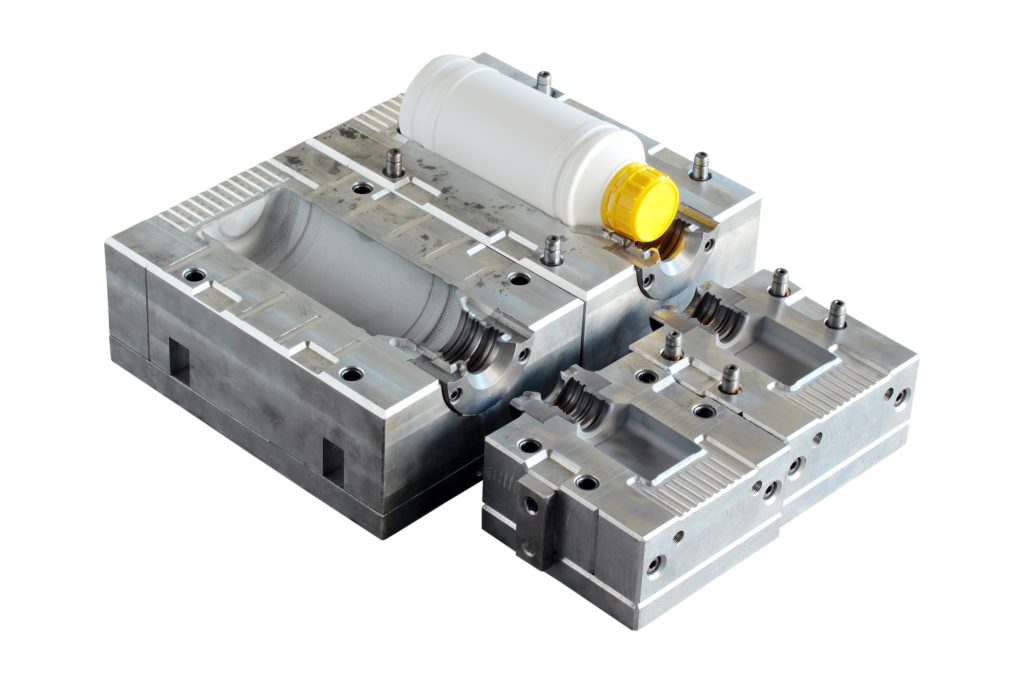
- Product Design: Good mold design is crucial to avoid defects such as air bubbles, burrs, and burn marks.
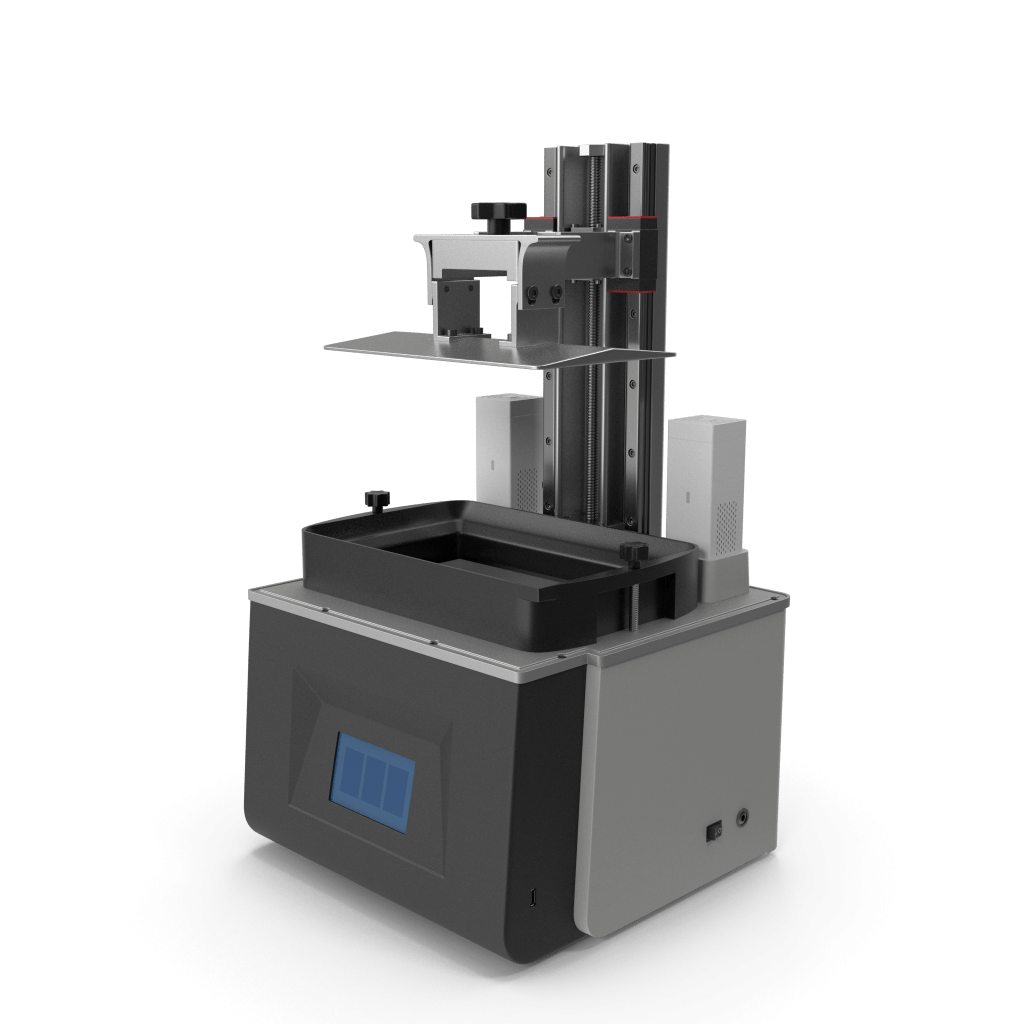